Stay Warm With These Heater Tips
February 26, 2020
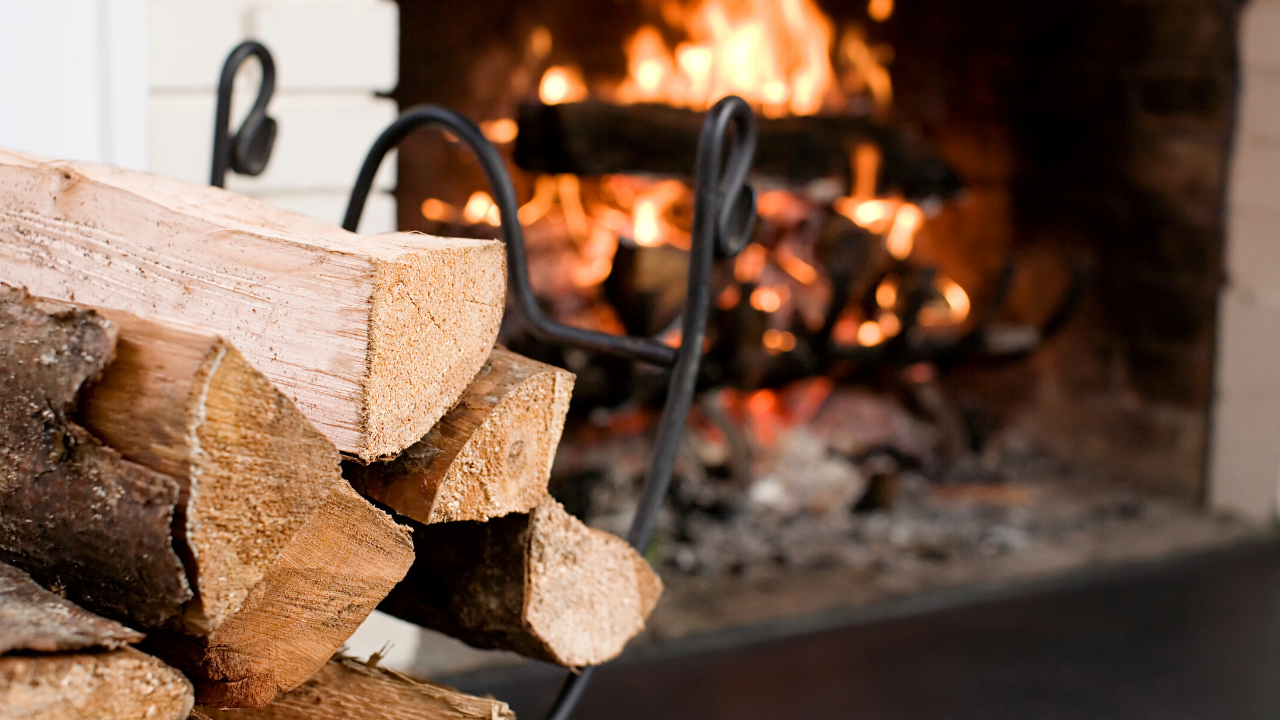
During the winter months, most manufactured homeowners see a spike in their utility bills. In fact, according to a report issued by the U.S. Energy Information Administration, heating accounts for as much as 41.5% of the average household utility costs in the winter.
As winter isn't over yet, which means that cold fronts with low temperatures, freezing rain and snow could still sweep across the country, it's not too late to look for ways to heat your manufactured home more efficiently and lower your utility bills.
Before you turn up the thermostat, we advise you to try the following three tips to keep your manufactured home warm in the winter and cut back on your heating bills.
Tip #1: Clean or Replace Your Heater's Air Filter
Besides reducing dust in your manufactured home and keeping your heater in good working condition, cleaning or replacing the air filter regularly could reduce energy consumption by 15%, according to EERE.
Regardless of the type of heating system, you have in your manufactured home, it's important to clean or replace the air filter at the beginning of each heating season. Additionally, EERE recommends cleaning or replacing the filter once a month during times of continuous use. Doing so will keep your system operating at peak efficiency, which could translate into lower utility bills.
Replacing or cleaning the filters regularly also prevents premature system failure due to dirt accumulation. If the filter becomes clogged with dust and debris, your heater will need to work harder and for longer periods of time. This can put extra strain on system components. In addition to consuming more energy, continuing to run your heater in this condition could do tremendous damage to it.
Depending on the type of heater, the filter may be located in the upper or bottom blower compartment, or in the filter rack inside the unit. If you're unable to locate the air filter, you can always call a professional to come and replace or clean your heater's filter, and inspect the ductwork, vents, and other components for any issues that may decrease the efficiency of your heating system.
Tip #2: Clean Your Air Ducts and Vents
In manufactured homes, the ductwork is either located underneath the floor or suspended above the ceiling. Because air ducts and vents allow your heating system to carry the heated air from the unit to every room in your manufactured home, cleaning your ductwork and vents regularly is critical to improving indoor air quality.
In addition to affecting your indoor air quality, dust and dirt accumulation inside the air ducts and vents will eventually decrease the airflow, restricting the heat output and reducing your heater's efficiency rapidly. The consequences of dirty ductwork are similar to those of clogged air filters: the heater will need to work harder and for longer in order to match the thermostat setting. By keeping your air ducts and vents clean, you can maximize your heater's efficiency, while lowering your energy bills.
Whether you have an HVAC system, a furnace or a heat pump, opening your vents all the way and removing any objects that may obstruct the airflow coming from them could also improve the energy efficiency of your heater. Conversely, if you own a new manufactured home or a pre-owned unit that was retrofitted with a ductless, mini-split heat pump, you don't need to worry about cleaning the air ducts and vents. Also known as “zoned HVAC systems” or “mini splits”, these pumps don't require ductwork to distribute the heated air to different areas of your manufactured home.
Tip #3: Insulate Your Ductwork
To ensure that your manufactured home is heated efficiently, it's important toseal and insulate your ductwork*. This can be done by insulating the underbelly or the ceiling of your manufactured home, depending on where the ductwork is located. Insulating your ductwork could improve the efficiency of your HVAC, furnace or heat pump up to 20%, according to Energy Star.
If you have a heating system that's attached to ductwork, you should also inspect the areas where the two meet. A bad connection between the heating system and the ductwork will result in air leaks, which may reduce the amount of airflow in the ductwork, preventing the system from running efficiently. Consequently, your manufactured home may not get warm enough, even though your energy bills remain high.
Scheduling a maintenance appointment with a technician every fall can help you get your heater ready for the cold weather and prevent unexpected breakdowns. The technician is the only professional able to inspect your entire heating system, including ductwork and vents, replace or clean the air filters, lubricate system components, and check for air leaks or any other damage that may decrease your heater's efficiency.
* For more information about the benefits of sealing and insulating your manufactured home's ductwork, we recommend checking the Duct Sealing Fact Sheet, published by Energy Star.